Key Takeaways
- Technical Fundamentals: Multilayer PCBs consist of 3+ conductive copper layers separated by insulating materials, enabling complex interconnections in compact form factors ranging from 4-layer consumer designs to 32+ layer advanced systems.
- Performance Advantages: Delivers enhanced signal integrity, 15 dB less electromagnetic radiation than two-layer boards, higher component density, improved durability, and significant space efficiency through vertical circuit stacking.
- Critical Applications: Essential for medical devices (ISO 13485), 5G telecommunications infrastructure, industrial control systems, automotive electronics, AI/IoT devices, and power electronics requiring high reliability.
- Manufacturing Capabilities: Support up to 68 layers (prototyping) with 2.0/2.0 mil line/space precision, ±5% impedance control, and multiple material options including FR4, high-speed, and Rogers substrates.
- KINGBROTHER‘s 28 years of expertise and comprehensive certifications ensure reliable multilayer PCB manufacturing for demanding applications across diverse industries.
Introduction
In today’s rapidly evolving electronics landscape, the demand for compact, high-performance devices continues to drive innovation in printed circuit board (PCB) technology. Multilayer PCBs have emerged as the backbone of modern electronic systems, enabling manufacturers to pack more functionality into smaller spaces while maintaining superior performance characteristics.
Whether you’re developing 5G telecommunications equipment, medical devices, or AI-powered IoT systems, understanding these advanced circuit boards is crucial for successful product development.
This comprehensive guide explores the fundamentals, benefits, and applications of multilayer designs, while highlighting how KINGBROTHER’s 28 years of manufacturing expertise help create cutting-edge devices that support and enhance diverse industries.
What is a Multilayer PCB?
A multilayer PCB is a printed circuit board consisting of three or more conductive copper layers separated by insulating materials (dielectrics). Unlike single or double-layer boards, these advanced circuits stack multiple layers to create complex interconnection patterns while maintaining a compact form factor.
The multilayer PCB construction features inner layers completely enclosed within the PCB structure. This design provides enhanced functionality and performance compared to simpler alternatives.
Multilayer PCB Layer Count (4-Layer, 6-Layer, 8-Layer, 12+ Layer PCBs)
These boards are classified based on their layer count, with each configuration offering specific advantages:
- 4-Layer PCBs: The most common entry-level multilayer design, ideal for consumer electronics and simple industrial applications
- 6-8 Layer PCBs: Perfect for telecommunications equipment, automotive electronics, and moderate-complexity designs
- 10-16 Layer PCBs: Suitable for high-speed computing, advanced medical devices, and complex industrial control systems
- 20+ Layer PCBs: Used in sophisticated applications like high-end servers, aerospace systems, and advanced telecommunications infrastructure
KINGBROTHER’s advanced multilayer PCB manufacturing process extends this count up to 32 layers for mass production and an impressive 68 layers for prototyping, enabling support for even the most demanding applications.
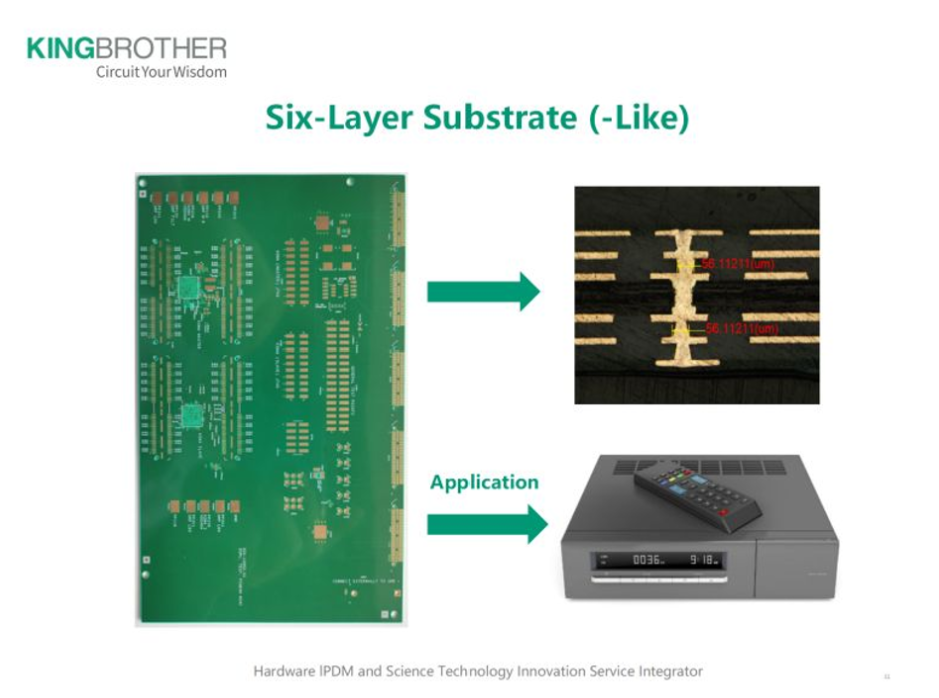
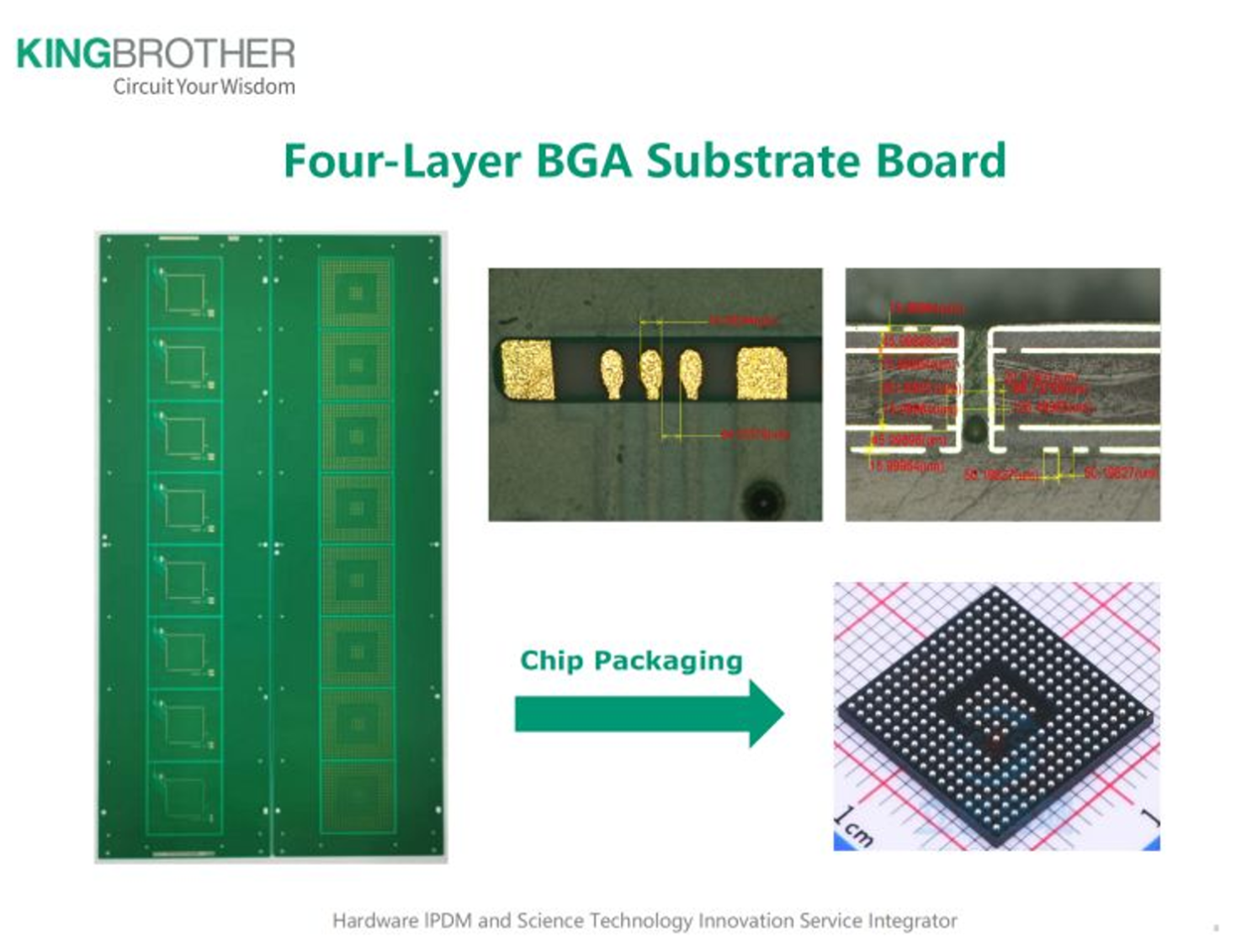
Construction Process and Materials
The multilayer PCB assembly process involves several critical steps that transform individual layers into a unified, high-performance circuit board:
- Inner Layer Preparation: Individual copper-clad substrates are etched to create the required circuit patterns.
- Layer Stacking: Alternating conductor and dielectric layers are precisely aligned and stacked.
- Lamination: The stack undergoes high temperature (typically 170-180°C) and pressure to bond all layers.
- Drilling: Through-holes and vias are drilled to establish interlayer connections.
- Plating: Conductive plating creates electrical connections between layers.
- Surface Finishing: Final treatments are applied for component mounting and environmental protection.
Multilayer PCB Design Specifications & Technical Capabilities
Understanding the technical limits and capabilities of PCB multilayer design is essential for successful project planning. KINGBROTHER offers industry-leading specifications across multiple categories.
Layer Count Specifications (4-32+ layers)
FR4 Standard
- Mass Production: Up to 32 layers
- Prototyping: Up to 68 layers
Rigid-Flex Combinations
- Mass Production: Up to 20 total layers (12 flex layers)
- Prototyping: Up to 32 total layers (30 flex layers)
High-Frequency Hybrid
- Mass Production: Up to 20 layers
- Prototyping: Up to 28 layers
PTFE Materials
- Mass Production: Up to 16 layers
- Prototyping: Up to 24 layers
HDI Technology (High Density Interconnect – using microvias for increased routing density)
- Mass Production: Up to 26 layers with 4-step HDI
- Prototyping: Up to 30 layers with any-layer HDI
Trace Width and Spacing Requirements
Precise control over trace dimensions ensures optimal signal integrity and electromagnetic compatibility in multilayer PCB production.
Minimum Line Width Capabilities
Standard PCB
- Mass Production: 2.5/2.5 mil (0.063/0.063mm)
- Prototyping: 2.0/2.0 mil (0.051/0.051mm)
IC Substrate
- Mass Production: 35/35 μm
- Prototyping: 25/25 μm
Line Spacing Specifications
Same Network Via Spacing
- Mass Production: 0.2mm
- Prototyping: 0.13mm
Different Network Via Spacing
- Mass Production: 0.25mm
- Prototyping: 0.20mm
Hole to Conductor Spacing (≤10 Layers)
- Mass Production: 0.15mm
- Prototyping: 0.125mm
Hole to Conductor Spacing (>10 Layers)
- Mass Production: 0.18mm
- Prototyping: 0.15mm
Maximum PCB Dimensions and Panel Sizes
Rigid Board Maximum Size
- Mass Production: 550mm × 620mm (21.7″ × 24.4″)
- Prototyping: 550mm × 900mm (21.7″ × 35.4″)
Double-Sided Flexible Board
- Mass Production: 1250mm × 200mm (49.2″ × 7.9″)
- Prototyping: 2450mm × 100mm (96.5″ × 3.9″)
Maximum Board Thickness
- Mass Production: 6.5mm (0.26″)
- Prototyping: 12mm (0.47″)
Aspect Ratio for Drill Holes
Aspect ratio refers to the relationship between hole depth and diameter, critical for reliable plating in multilayer PCB fabrication.
Through Via
- Mass Production: 16:1
- Prototyping: 25:1
Blind Via (Laser Drilling)
- Mass Production: 0.8:1
- Prototyping: 1:1
Material Options (FR4, High-Speed Materials, Rogers)
KINGBROTHER supports an extensive range of materials to meet diverse application requirements:
- Standard FR4 Materials: Shengyi S1000H, S1000-2M, S1150G, S1170G; TUC TU752, TU865; ITEQ IT158, IT180A
- High-Speed Materials: Shengyi S7439, S6B, S6N, S8GN, S9GN; Panasonic M6, M7N, M8N; TUC TU872-SLK, TU863+, TU883, TU933+
- High-Frequency Materials: Rogers RO3003, RO4000 series; Taconic TLY-5, TLX-8, TSM-DS3; Shengyi SG220/255/300 series
Types of Multilayer PCBs
The variety of available configurations allows designers to optimize their multilayer PCB boards for specific performance requirements and cost constraints.
Standard Multilayer PCBs
Standard designs using FR4 substrates form the foundation of most electronic devices. These boards offer excellent electrical properties, mechanical stability, and cost-effectiveness for applications not requiring specialized performance characteristics.
HDI (High Density Interconnect) Multilayer PCBs
HDI technology enables higher circuit density through microvias, buried vias, and sequential build-up processes.
Key HDI multilayer PCB Capabilities:
- Microvia Technology: Minimum 0.06mm laser-drilled vias (prototyping) / 0.10mm (mass production)
- Sequential Lamination: Up to 4-step HDI for mass production, any-layer for prototyping
- Signal Transmission Rate: Up to 25 Gbps (mass production) / 112 Gbps (prototyping)
Multilayer Rigid-Flex PCBs
Combining rigid and flexible sections, these boards enable three-dimensional packaging and eliminate connectors in many applications. This design supports complex geometries with varying layer counts between rigid and flex sections.
High-Speed Multilayer PCBs
Designed for applications requiring superior signal integrity, these boards utilize specialized materials and design techniques to minimize signal loss and electromagnetic interference at high frequencies.
PTFE Multilayer
For demanding RF and microwave applications, PTFE-based designs provide excellent dielectric properties and thermal stability.
Metal-Core Multilayer
Incorporating metal cores for enhanced thermal management, these boards are ideal for high-power LED applications and power electronics.
Heavy Copper Multilayer
Supporting copper thicknesses up to 6 OZ (mass production) / 18 OZ (prototyping), these boards handle high-current applications while maintaining advanced functionality.
Advanced Multilayer PCB Board Combinations
Modern applications often require hybrid approaches that combine multiple technologies for optimal performance.
Hybrid Multilayer PCB Designs
- High-frequency + Standard FR4: Combining high-frequency materials for critical signal layers with cost-effective FR4 for power and ground planes optimizes both performance and cost.
- Rigid + Flex: Variable layer counts between rigid and flexible sections enable optimal mechanical and electrical design for complex assemblies.
- HDI + Standard Via: Combining microvias in high-density areas with standard vias elsewhere balances performance with manufacturing efficiency.
Embedded Component Multilayer
- Embedded Passives: Integration of capacitors, resistors, and other passive components within the PCB structure saves space and improves electrical performance.
- Substrate-like PCB: Advanced packaging substrate technology enables ultra-fine geometries for semiconductor packaging applications.
- Package Substrate Applications: Specialized designs for flip-chip and ball grid array (BGA) packaging requirements.
What is the Difference Between a Single-Layer and a Multilayer PCB?
Understanding these differences helps in selecting the appropriate technology for your application.
Performance Comparison Table
Feature |
Single-Layer PCB |
Multilayer PCB |
Layer Count |
1 |
3+ (up to 68) |
Side Mounting |
1 |
Both |
Circuit Density |
Low |
High |
Signal Integrity |
Limited |
Excellent |
EMI Performance |
Poor |
Excellent |
Size Requirements |
Large |
Compact |
Durability |
Low |
High |
Cost |
Low |
Higher |
Design Complexity |
Simple |
Complex |
Manufacturing Speed |
Fast |
Slower |
Maintenance |
Easy |
More complex |
Cost Analysis
While advanced designs require a higher initial investment, they offer superior value through:
- Reduced System Size: Eliminating multiple single-layer boards and connectors
- Improved Reliability: Fewer mechanical connections and solder joints
- Enhanced Performance: Better signal integrity reduces system-level debugging costs
Application Suitability
Single-layer PCBs remain suitable for simple, low-frequency applications (calculators, vending machines, printers, LED lighting systems).
However, advanced designs are essential for modern electronics requiring high performance, compact size, and complex functionality, such as defense systems, medical equipment, aerospace applications, and surveillance systems.
Benefits and Advantages of Multilayer PCBs
The advantages of these advanced circuits extend far beyond simple space savings.
Space Efficiency and Miniaturization
Multilayer PCB construction enables significant size reduction by stacking circuits vertically rather than expanding horizontally. This three-dimensional approach allows designers to pack more functionality into smaller footprints, crucial for portable devices and space-constrained applications.
Enhanced Signal Integrity
Dedicated power and ground planes in multilayer designs provide:
- Reduced Impedance: Lower power distribution impedance
- Controlled Impedance: Precise characteristic impedance control
- Reduced Crosstalk: Better isolation between signal layers
Improved EMI/EMC Performance
A strategic multilayer PCB design with proper power and ground plane placement produces 15 dB less radiation than a two-layer board. This significantly reduces electromagnetic interference and improves electromagnetic compatibility.
The planes act as shields, containing radiation from high-speed traces and providing better current return paths.
Higher Component Density
Multiple routing layers enable more complex interconnections, supporting higher component densities and more sophisticated circuit designs.
Greater Durability
Advanced boards withstand greater weight and higher levels of heat and pressure compared to simpler alternatives.
Flexible Construction
The multilayer PCB fabrication process offers designers a myriad of options to create custom multilayer PCBs, including changing the copper thickness, number of layers, and more.
Multilayer PCB Applications by Industry
Different industries leverage these advanced circuits to solve unique challenges and meet specific performance requirements.
Medical Device PCBs
Medical applications demand exceptional reliability and often require compliance with stringent regulations like ISO 13485.
Key Features:
- Biocompatible Materials: Suitable for implantable and patient-contact devices
- High Reliability: Extended operational life for critical medical equipment
- Regulatory Compliance: Full traceability and quality documentation
Telecommunications and 5G PCBs
5G infrastructure requires high-frequency capabilities and exceptional signal integrity.
Our Solutions Support:
- High-Frequency Performance: Materials optimized for millimeter-wave applications
- Signal Integrity: Controlled impedance and minimal loss
- Thermal Management: Enhanced heat dissipation for high-power applications
Industrial Control System PCBs
Industrial environments demand robust, reliable PCBs capable of withstanding harsh conditions.
Design Features
- Extended Temperature Range: Operation from -40°C to +125°C
- Enhanced Durability: Resistant to vibration, shock, and chemical exposure
- Long-Term Availability: Component lifecycle management for extended product lifecycles
Power Electronics PCBs
Power applications require specialized design considerations.
Specialized Capabilities:
- Heavy Copper: Up to 18 OZ copper thickness for high-current handling
- Thermal Management: Advanced thermal via and heat spreading techniques
- High Voltage: Specialized materials and spacing for high-voltage applications
AI and IoT Device PCBs
Emerging AI and IoT applications demand unique solutions.
Key Requirements:
- Miniaturization: Ultra-compact designs for wearable and embedded devices
- Low Power: Optimized for battery-powered applications
- High-Speed Processing: Support for advanced processor requirements
Automotive Electronics
Automotive applications require exceptional reliability and compliance with automotive standards.
Critical Features:
- Temperature Cycling: Survival in extreme automotive temperature ranges
- Vibration Resistance: Robust mechanical design for automotive environments
- Quality Standards: Compliance with ISO/TS 16949 automotive quality requirements
KINGBROTHER’s Multilayer PCB Manufacturing Capabilities
Our state-of-the-art facilities and comprehensive expertise in the manufacturing of multilayer PCBs enable industry-leading performance across all specifications.
Technical Specifications and Limits
Our core capabilities include:
- Layer Count: Up to 68 layers (prototyping) / 32 layers (mass production)
- Minimum Feature Size: 2.0/2.0 mil line/space (prototyping)
- Impedance Control: ±5% (prototyping) / ±10% (mass production)
- Surface Finishes: HASL, OSP, ENIG, ENEPIG, Hard Gold, Soft Gold
Industry Expertise and Certifications
As a manufacturer of multilayer PCBs, we maintain comprehensive quality certifications to ensure reliable, compliant manufacturing:
- ISO 9001: Quality management systems
- ISO 14001: Environmental management
- ISO 13485: Medical device quality management
- ISO/TS 16949: Automotive quality standards
- UL: Safety certifications
Quick-Turn Prototyping Services
Rapid prototyping capabilities enable accelerated product development:
- 24-48 Hour Multilayer PCB Prototypes: Express services for urgent projects
- Design for Manufacturing (DFM): Optimization recommendations to improve manufacturability
- Flexible Order Quantities: No minimum order quantities for prototyping
Get Started with the Best Multilayer PCB Manufacturing Service in Your Sector
Advanced circuit boards are the foundation of modern electronics, from 4-layer consumer devices to 32-layer telecommunications infrastructure. With 28 years of experience and capabilities spanning up to 68 layers, KINGBROTHER delivers the expertise and manufacturing excellence needed for medical devices, 5G equipment, AI systems, and beyond.
Ready to bring your design to life? Contact our technical team to discuss your requirements and discover how our advanced capabilities can accelerate your time-to-market while optimizing costs.